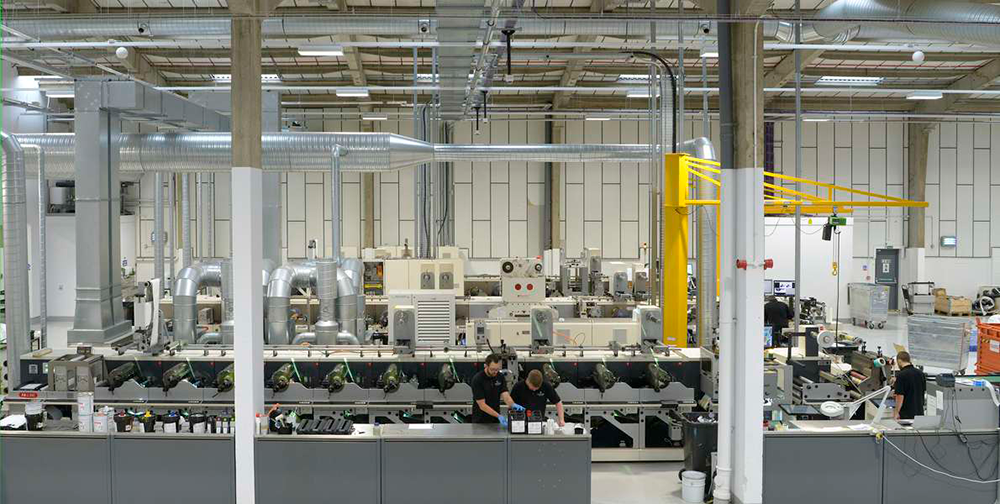
Royston Labels invests in the future with state-of-the-art new equipment
In the last 12 months Royston Labels has benefitted from a huge package of investment, allowing us to move to brand new spacious premises and make significant additions to our production capabilities.
Though we’ve only been in our new building for a few months, we’re already seeing huge leaps forward in efficiency and productivity, made possible by equipment such as our Nilpeter FA-4* (Asterisk). The 10-colour Asterisk is a state-of-the-art press that offers impeccable tolerance standard and dot gain coverage – in other words, a fantastic finish every time. Safe and user-friendly with an ergonomic design, this press promises a truly optimised performance.
Our Asterisk is equipped with the powerful EC2 UV curing system, which is manufactured by GEW. The EC2 is a low-energy, low-cost curing system that allows us to easily switch between standard and LED lamps (depending upon the requirements of a specific label) simply by changing cartridges
The Asterix, which can be controlled remotely via an iPad, can also deliver high-quality embellishments via its rotary hot foil, cold foil and laminating units. It has drop in screen compatibility and an AVT 100% web inspection system, which lets us control every aspect of the production process and avoid costly errors.
The cherry on the cake is that the Asterix boasts running speeds in excess of 100 metres per minute, allowing us to deliver the superior quality our customers demand with both speed and precision. Two of our printing experts, Jason and Pawel, have been working with the Asterix since it was installed and are blown away by the fast turnarounds and high quality finishes.
We’ve also boosted our capabilities in high-end embellishment, with the addition of a Pantec Rhino flatbed hot foil and embossing unit. The Rhino allows us to apply multiple foils and crisp, detailed embossing in a single pass. It also features a unique revolving head to minimise foil usage and maximise productivity.
Our digital department has been similarly strengthened with the arrival of a second Digicon finishing line. The Digicon Lite, equipped with two flexo stations and Fast Track die cutting system, is now working alongside our existing Series 3 Digicon, and has allowed us to maximise production from our Screen L350 UV digital inkjet press.
This investment in capital equipment, coupled with the move to a modern new facility with everything under one roof, means we are ideally placed to meet the ever increasing demands of today’s labelling sector.
If you’d like to find out more about our capabilities, and how our talented, creative team can help bring your dream label to life, get in touch today on 01763 212020.
Source: Royston Labels