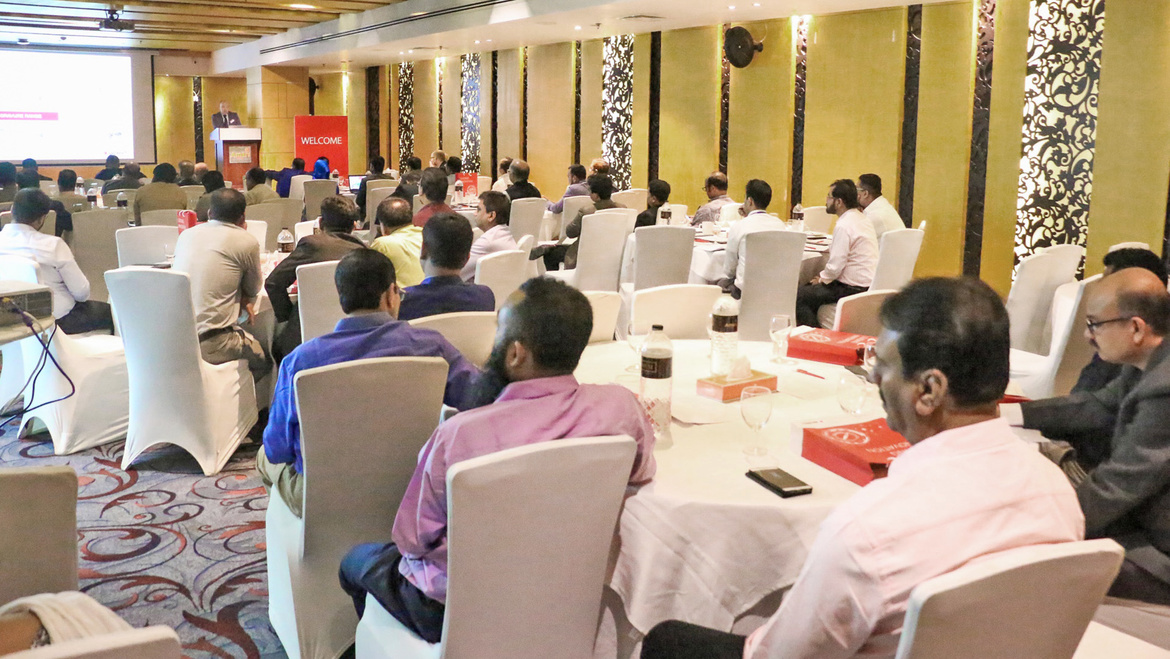
The BOBST & Partners roadshow was held at the Hotel Amari in Dhaka, Bangladesh
BOBST technology a favorite with Bangladesh flexible packaging converters
The appeal of BOBST technology in Bangladesh and in the Indian subcontinent continues to be strong and thriving. The first electronic line shaft ELS gravure printing press in Bangladesh was from BOBST and more ELS presses have been installed over the past 6 years or so.
If rotogravure is still the predominant printing process for the flexible packaging sector, CI flexo has also started making inroads for products like edible oil pouches and printed PE for diapers. The development of reverse flexo printing as an alternative to gravure is however hindered by lack of skilled operators and issues with flexo pre-press and inks.
Nevertheless, despite the challenges converters are confronted with while the local infrastructure is being revamped, the flexible packaging sector is growing and investing in advanced technology.
This was evident during the first roadshow dedicated to flexible packaging that BOBST and industry partners Atlas Converting, Macchi, Siegwerk and Rossini held recently in Dhaka. The event provided a forum for an overview of the latest technologies and consumables all along the value chain that generated intense interaction between the panel speakers and the attending delegates that delved deeper into the topics presented. Over 30 companies attended representing leading converters, brand owners and packaging consulting firms.
“The local shortage of experienced operators makes all systems that reduce errors and variables due to manual settings very appealing” explains Avra Mitra, Senior Manager Key Accounts, Bobst India, “BOBST equipment for gravure and flexo printing, laminating, coating and vacuum metallizing delivers the kind of automation that ups productivity and enables sustainable operation, along with easy HMI and connectivity features that ensure production of high quality flexible packaging”
Hence the solutions that drew most interest at the roadshow included BOBST implementation of the Extended Color Gamut (ECG) along with the smartGPSTM system for offline set-up and automatic adjustment of printing pressure and register on the 20SEVEN flexo press, and the integration of the ELS and Registron® control for the fastest register correction on the range of gravure presses.
In converting, high on the agenda were the next generation of compact laminators offering fast and tool-less job changeovers, and vacuum metallizers. The latter includes process solutions like the AluBond® patented technology that significantly improves barrier levels on BOPP and CPP films, and the Integrated AlOx Conversion Solution that maintains barrier levels of the coated film during printing and converting.
Waste management and plastics recyclability drive the global industry and are major requirements from brand owners. This is a challenge in the future of the Bangladesh industry, but forward-looking converters are already installing equipment that is ready to meet future local market requirements and regulations. This includes latest generation laminating and extrusion laminating machines that offer wider flexibility in substrate handling and sustainable operation to produce packaging that meets international standards.
The extent of BOBST commitment to technical support is another reason behind the reputation that BOBST enjoys with Bangladesh leading flexible packaging converters. There are currently twenty four highly skilled field engineers for the vacuum metallizing, gravure, flexo and coating and laminating machines installations in the Indian subcontinent. These specialized teams, that can also offer expert advice and training in process optimization, are instrumental in supporting the successful and sustainable growth of local industry.
Bobst Mex SA, Switzerland
Source: Bobst